全体の断面寸法が小さい鋼製品の曲げ加工は、通常、冷間状態で行われます。 このプロセスは、変形したワークピースの縦軸または横軸の不可逆的な変化で構成されます。
曲げのタイプは次のパラメータで異なります。
プロファイルツールを使用した曲げ技術
以下で説明するすべてのプロセスは、専用のツールを使用して実行されます。 スタンプ。 曲げ金型の作動部分は次のとおりです。 パンチとマトリックス。 パンチ– スタンプの可動部分は固定されています。 原則として上半分、スライダーが動くと前後に動きます。 マトリックス– スタンプの固定部分 – はスタンプの下半分にあり、機器テーブルに固定されています。
プロファイル工具によるスタンピングの精度は、次の要素によって決まります。
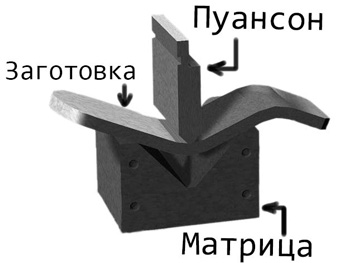
曲げパンチとダイの加工プロファイルを設計する場合、主な要素は技術力ではなく (すべての曲げオプションで小さなものです)、いわゆるワークピース金属の弾性残効です。 湧き出る.
バネの結果として、金属は常に元の形状に戻ろうとする傾向があり、この傾向の強さは塑性限界によって異なります。 軟金属(アルミニウム、銅、炭素含有率0.1%以下の鋼など) スプリングバックは 3 ~ 8%、真鍮、中炭素鋼、高炭素鋼 - 12 ~ 15%.
スプリングバックはいくつかの方法で考慮されます。
- 将来のスプリングバックを考慮した加工プロファイルを備えたパンチとダイの製造(たとえば、金属の予想されるスプリングバックが 10 0 でワークピースを 60 0 の角度で曲げる必要がある場合、工具プロファイルは 70 0 の角度で作成されます)。 バネ係数は材質とワークの厚みに応じて表から求められます。
- アンダーカット付きパンチの製作、変形した金属が流れる場所。 この場合、弾性余効力はワークピースの塑性変形の力によって中和されます。
- 追加のキャリブレーション遷移を導入することにより製品の追加刻印が発生した場合。 この方法は曲げ加工が複雑になるため非生産的です。
- 変形率を低減し、金属に負荷をかけたままにする変形部分の慣性力がなくなるまでしばらく放置します。 これは、油圧プレスまたは特殊なクランク ドライブを備えたプレスでのみ可能です。
曲げ工具の摩耗が不均一である場合: より集中的に消耗するパンチとダイ 元のプロファイルが変化している場所一方、周辺領域の抵抗ははるかに高くなります。 ただし、工具は修復または修理できます (ほとんどの場合、摩耗した部分は融着され、その後、適切なサイズに研磨されます)。
プラスチック材料の曲げ加工にパンチとダイスを使用し、 GOST 1435 に準拠した炭素工具鋼タイプ U10 または U12 から作られています。。 引張強度を高めた材質のワークをパンチやダイスで変形させます。 GOST 5950 に準拠した合金工具鋼タイプ 9ХС または Х12М.
金型で曲げるための主な種類の装置は次のとおりです。
- 機械駆動の垂直プレス ブレーキ (国内プレス業界では、これらの機械は I13_ _ と呼ばれ、最後の 2 桁は公称力を示します)。
- 横型プレスブレーキ(I12__シリーズ)。
- 万能マルチスライド自動板曲げ機(A72__シリーズ)。
プロファイル工具を使用して曲げる技術には限界があります。
- プレス機でスタンピングを行う場合、必ずステージが存在します。 リターンストローク、変形が起こらない場合、したがって 生産性が低下する;
- 1つで スタンプのセットパーツを作ることは可能です 厳密に定義された標準サイズ。 この状況を部分的に解決する方法は、プレス スライドの同じ値の作動ストロークを必要とする部品用に、プレス テーブル上に異なるパンチとダイのセットをいくつか設置することです。
- スタンプは技術的に複雑なツールです、そのコストはかなり高くなります。 これは最終製品の価格に悪影響を及ぼします。
- 断面形状を曲げる場合、ワークの断面形状が異なる箇所でクラックが発生する可能性があります。.
これに基づいて、非プロファイル工具を使用した曲げは、重要な部品生産プログラムにのみ使用する必要があります。
この曲げ方法は、次の用途に基づいています。 回転工具。 この場合、次のような変形が生じます。 連続的に回転するロール間の隙間にワークを通過させる。 ローラーは、そのような通過の結果として製品が必要な曲率を獲得するように配置されています。
長尺製品の高品質曲げ – チャネル、I ビーム、角度– この場合、結果はワークピースの断面パラメータの影響をまったく受けないため、この方法でのみ可能です。
薄板金属の加工では円に沿った曲げが発生し、長尺鋼材の加工では作業ロール間の距離を変えることで設定される円弧に沿って曲げが発生します。
最も普及している 3ロールシートベンディングマシンとセクションベンディングマシンを購入。 2 つのロール (下部) はサポート、3 つ目 (上部) は圧力です。 ローラーベンディングマシンの分類は、次の基準に従って行うことができます。
- 装置の垂直軸に対するロールの位置に応じて、対称および非対称になります。対称的に配置されたローラーでは、加圧ローラーは厳密に中央に配置され、非対称設計では、加圧ローラーはサポート ローラーの 1 つの上に配置されます。
- ロールの幅に合わせて、これが機器の技術的能力を決定します。ロールが長いほど、この設置でシートをより広く曲げることができます。
- 追加ロールの有無に応じて、メインのものの前または後にインストールされます。 このような装置は、製品の曲げだけでなく、その後の矯正も行います。
- ワークロールの相対位置に応じて、水平面または垂直面にあります。 後者はあまり便利ではありませんが、結果として平面上の装置全体の寸法が縮小されるため、場合によっては推奨されます。
回転曲げ中、力は接触点ではなく円弧に沿ってかかるため、ローラーにかかる比負荷が小さく、第一に耐久性が向上し、第二に安価な工具鋼の使用が可能になります。彼らの製造のために。
スタンプツールとは異なり、ロールツールは汎用品であるため、回転曲げはあらゆる最終製品生産プログラムに効果的です。
シート曲げ機とセクション曲げ機の一連の操作。 シェルの曲がり。
対称配置のワークロールを備えたシート曲げ装置での曲げには、以下のものが含まれます。 次の段階:
- シートの詰め替えワークピースの前端が 2 番目のサポート ローラーの上にあるように、ローラー間のスペースに押し込みます。
- トップロールを下げる曲げプロファイルの必要な曲率が保証される位置まで。
- ドライブの電源を入れるその結果、シートは摩擦力によってローラーに捕らえられ、作業領域を通過し、必要な形状が得られます。
- 次のワークの補充、変形サイクルの繰り返し。
作業エリアを通過した製品 シートの前後端が変形しないサポートローラー間の距離の半分に等しい量だけ。 裾上げは手作業なので不便です。 したがって、ワークピースの全長に沿ってプロファイルを曲げる必要がある場合は、次の方法を使用する必要があります。 非対称レイアウトの回転機械。 この場合、後端は曲がることが保証されており、前端はシートを裏側から挿入するだけで十分です。 したがって、から 板金それが判明 シェル(開いた円筒形または円錐形の構造要素)。
さまざまな厚さのシートを曲げることができるように、機械には以下の機能が装備されています。 下部ローラー間の距離を調整する。 これを行うには、これらのロールの軸が回転するベアリングを移動します。 厚みのあるワークを回転させる場合に必要となる、ロールを大径工具に交換することも可能です。
選別機も同様の方法で動作します。 また、3 ロール設計で作られており、 次のユニットで構成されます。
- ベッド.
- ローラー、その作業プロファイルは長い製品のセクションに対応します。
- サイドローラー、ワークの動きの真直性を確保します。
- ワークピースの横方向の動きを制限するクロスバー (チャネルなどの対称プロファイルの場合、クロスバーは非作業位置に移動します)。
- 補充機構ロール間の作業スペースにプロファイルを挿入します。
- 電気モーター.
- 中間ギア.
- ドライブアクティベーションシステム.
ソートベンディングマシンは、ねじ機構のハンドホイールを使用して必要な曲げ半径に調整されます。 小型の標準サイズの長尺製品は、水平ワークロールを備えた機械で曲げられます。 垂直レイアウトの選別機は、より汎用的であると考えられています。
国産ロータリーベンディングマシンのマーキング:
- I22_ _ - 3 ロールシート曲げ;
- I42_ _ - 4 ロールシート曲げ;
- I32_ _ — 3 ロールソート曲げ。
- I33 - マルチロール曲げグレード。
金属の曲げは、修理時、部品の破片やオートバイを新しく作るとき(腐ったものと交換するため)、または車体やオートバイの付属品(カスタム)の新しい板金部品を最初から作るときに最も一般的な作業です。 。 まあ、あるいは単純に日常生活のさまざまな部品の製造において。 この記事では、より初心者向けに、板金を曲げる基本的なテクニックと、 金属を剥がす手作業のほか、この問題に最も一般的なツールや機器も使用できます。
板金や帯状の金属を曲げる加工に関する基本的な情報です。
曲げプロセス中、金属 (シート、ロッドなど) は引張力と圧縮力の同時作用にさらされます。 同時に金属部品の外側や屈曲点では金属繊維が引き伸ばされて長さが長くなります。 そして、部品の内側では、逆に繊維が圧縮され、その長さが短くなります。 また、曲げの瞬間には中立層 (中立線 - 図 1 を参照) のみが引張も圧縮も受けず、部品を曲げた後でも中立線の長さは変わりません。
ワークピースを曲げた後の変形による金属の構造の変化: a - 伸張された繊維、b - 中立層、c - 圧縮された繊維。
図 1 では、部品が曲がった場所での金属の構造の変化がはっきりと確認できます。図で文字 A (ゾーン A) でマークされている金属の上層は引き伸ばされ、下層は伸びています。 、文字 B (ゾーン B) でマークされている部分は、著しく圧縮 (変形) されています。 ゾーン B (部品の中央部分、いわゆるニュートラル ライン内) の金属の構造は、実質的に変化しません。
金属を曲げるときは、曲げ応力が材料 (金属または合金) の弾性限界を超えない場合、部品の変形は弾性となり、曲げ力の適用を停止すると部品は変形することを考慮する必要があります。元の形(形)に戻ります。 また、部品に特定の望ましい曲率を得るには、部品の弾性限界を超える曲げ力を加える必要があります。そうすると、部品の変形はすでに塑性化し、部品は元の形状を変えてしまいます。
板材の曲げ加工では、塑性変形に必ず弾性変形が伴うため、ある角度まで曲げた部分では、曲げ力の圧力がなくなった後(応力がなくなった後)、バネ現象が発生します。曲げ部分の曲げ角度は常にわずかに大きくなります。つまり、力の適用を停止した後、部分はわずかに真っ直ぐになります。
また、部品が真っ直ぐになる角度は、材料の弾性と厚さ、曲げ半径によって決まり、弾性反動(バネ作用)があるため、弾性変形角度と呼ばれます。 金属を曲げてさまざまな部品を製造する場合、さまざまな金属や合金のばね特性 (当然ながら異なります) を常に考慮する必要があります。
しかし、実際には、一般に、さまざまな材料のばね角度を事前に正確に決定することはそれほど簡単ではないため、曲げによる精密部品の製造を目的とした設備は複数回修正する必要があります。 しかし、必要な正確な角度と曲げ半径を生み出す別のタイプの曲げもあります。 これは、いわゆる張力を伴う曲げのタイプであり、曲げるときに部品は追加の張力の助けを借りて伸びることになり、同時に部品の断面のすべての繊維が張力を受けます。
この場合、断面のわずかな減少のみが観察され、角度と曲げ半径は変化しません。 金属加工では、単純な曲げの原理に基づく、つまり部品の材料のバネを考慮した曲げ加工が最も一般的です。
金属を手作業で曲げる基本的なテクニック。
手曲げ薄い材料で作られた部品は、打撃ではなく平滑化によって実行されます。 厚さ0.5 mmを超えるストリップまたはシート材料(および直径4 mmを超えるロッド)からの金属ブランクの曲げは、ハンマーブローを使用してマンドレル上で実行されます。 この場合、使用するマンドレルの形状は、当然ながら、曲げプロファイルの形状に対応し、材料の変形を考慮する必要があります。
異なる金属 (合金) のシート材料を冷間曲げする場合は、合金によって異なる可能性がある最小半径を常に考慮する必要があります。 これを下の表に示します。
表に示されている半径よりも小さな半径を持つある種のプロファイル部品を製造する必要がある場合、そのような部品を真っ赤に加熱し、その後にのみ曲げを行う必要があります。 ワークにクラックや破損が生じる可能性があります。
そしてもう1つの重要なニュアンス:上の表は、巻かれた繊維に沿ったシート材料の最小曲げ半径の値を示しています。 丸めた繊維にまたがって金属 (合金) を曲げる場合、加熱することなく、曲げ半径を約 2 倍に増やすことができます (ワークピースに損傷を与えることなく)。 これが明らかだといいのですが、次に進みましょう。
部品を90度の角度で曲げます。
曲げる前に、曲げ線がバイスのジョー (または軽合金のジョー) の上端のレベルに位置するように、ワークピースをバイスでクランプする必要があります。 この場合、曲げ加工は通常2段階で行われる。
まず、ワークの上部(図 2 a を参照)をワークに対して 45 度の角度に配置されたハンマーで叩き、その後、バイスのジョーの下を角度は 90 度です (図 2 b を参照)。
当社の作業では、金属ハンマー(鋼製ワークピースの曲げ用)と木製、カプロロン、または銅ハンマー(軟質合金製ワークピースの曲げ用)の両方を使用します。これらは、軟質合金製ワークピースの滑らかな表面を損なうことがありません。
ただし、スチールハンマーを使用して部品の曲げ部分に角度を形成する方が良いです。ハンマーのストライカーの表面はわずかに球面で滑らかに研磨(鏡面)されています。 同時にハンマーヘッド全面でワーク(ジョー部分)に均一な打撃を加えます。
90 度 (直角) のいくつかの角度を持つワークピースの曲げは、通常、強力な万力でクランプされた特別なマンドレルで行われます。 マンドレルを使用して金属を曲げる場合、事前にワークに曲げ線をマーキングします。
作業では、通常、銅、カプロロン、または木製のハンマー (特に軟質合金で作られた部品) を使用して棚自体を部品に曲げ、その後鋼のハンマーで叩いて曲げ角度自体を形成します (打撃が加えられます)。マンドレルの端の領域、角の領域)。
鋼板製の部品を90度以外の角度で曲げる場合。
このような角度のブランクは、完成品の寸法とプロファイル(形状)に対応する寸法と形状の特別なマンドレル上で曲げられます。
たとえば、図 3 a に示す部品を線 aa および bb に沿って曲げるには、図 3 b に示すマンドレルを使用します。
このようなマンドレルでは、棚 1 はワークピースを線 bb に沿って曲げるときにワークピースを支持する役割を果たします。 また、棚 2 は、線 a-a に沿ってワークピースを曲げるためにワークピースの薄い端を支持する役割を果たします。
板金ブラケットの曲げ加工。
鋼板(より正確には鋼帯)からブラケットを曲げる場合、円筒形のマンドレル(基本的には必要な直径の通常の鋼棒)を使用します。
そしてもちろん、マンドレル (ロッド) の直径は、製造されるブラケットの溝のサイズに対応していなければなりません。
マンドレル上でステープルを曲げるときの作業の順序と打撃の方向は、図 4a と 4b に矢印で示されています。
短冊状の金属板で作られたクランプを曲げる作業です。
クランプを作成するには、まず必要な幅の鋼帯にマーカー (またはスクライバー) で曲げ点をマークします。 私たちの作業では、将来のクランプの穴の内径に対応する、必要な直径のロッドで作られたマンドレルを再び使用します。
マンドレル 1 を万力で垂直にクランプし (図 5 a を参照)、スチール ストリップに事前にマークしたマークに沿って、2 つのペンチを使用して、最初にクランプ ブランクをマンドレルに沿って曲げます (図 5 a)。
鋼板ブッシュの曲げ加工。
この形状の大部分はローラーを使用して作成できますが、小さなブッシュはローラーを使用して作成できませんが、そのような部分は、再度万力と必要な直径の円筒形のマンドレル (ロッド) を使用して、以下に説明するように作成できます。 。
マンドレル上の円筒ブッシュを曲げるときの一連の作業 (遷移) を図 6a、b、c に示します。
このような部品を作成する場合は、強すぎて不正確なハンマー打撃により部品が変形する可能性があるため、注意が必要であることに注意してください。
初心者の場合、特に軟質合金や薄すぎるシート材料で作られたワークピースには、柔らかいハンマー (銅、カプロロン、テキストライト、または木材) を使用することをお勧めします。
治具にも柔軟に対応します。
金属を曲げるための最も単純な装置は、もちろん、手作業のコストを削減し、同時に曲げの品質を向上させます。 たとえば、ドア用のヒンジ付きキャノピー (ヒンジ) を作成する場合、図 7 a に示す単純な装置を使用すると、作業が大幅に容易になり、品質が向上します。
本体 1 のこのデバイスにはスロット 3 があり、そこに板金 2 のストリップを挿入します。
次に、鋼ストリップの下端をワークピースの本体に開けられた穴に当てながら、ワークピースの上端を優しく均等に打撃します (打撃の代わりに、バイスや のジョーの圧力を使用できます)。デバイスを押し込み、ストリップの上端に圧力をかけると、固定具の穴の直径を繰り返しながら、ストリップの底部で曲がり始めます。
図 7a に示す別の単純なデバイスを使用すると、シート メタルまたはストリップから成形部品を作成できます (シートまたはストリップは、デバイスの幅によって異なります)。 図形部分 (耳) は 2 つのステップで作成されます。最初のステップは図 7 b に示され、2 番目のステップは図 7 c に示されます。
まず、鋼ストリップ 1 が固定具 3 (いわゆるマトリックス) に配置され、ワークピースはマンドレル 2 (いわゆるラム) の圧力下で曲げられます。 さて、第 2 ステップでは、最終的にワークをバイスで圧着します (図 7 c)。 パンチの幅は、マトリックスの溝の幅より、曲げられるシート材料の 2 つの厚さだけ狭くなければならないことに注意してください。
棒材を90度曲げる.
3 mm 以下のワイヤーで作られた部品の曲げはペンチで行うことができ、3 mm を超えるワイヤー (ロッド) はバイスまたはマンドレルで曲げます。 たとえば、ブラケットを作成する場合、まずワークピースを必要なサイズに切断し、曲げ点に印を付けてから、マンドレル(立方体)を通してバイスに垂直にクランプします(図を参照)。 8a.
次に、ハンマーを使用して、ワークピースの最初の端をマンドレルの上面に完全に押し付けられるまで曲げます(図 8 b を参照)。
次に、ワークピースを裏返し、部品のもう一方の端を同じように曲げます (図 8c)。
もちろん、マンドレルの形状と寸法はブラケットのサイズに依存し、ブラケットの幅が広いほどマンドレルの幅も広くなります(逆も同様)。
マンドレルにアイレットを作成します(ロッドまたはワイヤーを曲げます)。
細い針金でできたハトメは、もちろんペンチ(ラジオペンチ)で曲げることも可能です。 ただし、ワイヤの太さが 3 mm を超える場合、またはより太いロッドの場合は、万力にクランプされた丸いマンドレル上でアイを曲げることが可能です。 まず、必要な長さにカットした部分に、将来の耳の円周の半分に等しい端からの距離に印を付けます(印を付けます)。
次に、前にマークしたマークがバイスのジョーの上面のレベルに正確に位置するように、ワークピースを垂直位置でバイスにクランプします。これを図に示します。 9a.
これで、ワイヤーがマンドレルに接着している場所をストライカーで叩き、目の半分が曲がるまでハンマーでワイヤーを曲げることができます(この場合、曲がったワイヤーはバイスの反対側のジョーに当たります) - 図9a)。
耳の半分が曲がったら、今度はワークピースをマンドレルで押し、ひっくり返して再度クランプし(図 9 b を参照)、ハンマーで叩いて耳の後半を曲げる必要があります。 。 ここで残っているのは、ハンマーでの打撃と万力のジョーの絞りを組み合わせて、最終的に耳の輪郭を形成することだけです。この操作は図 9 d に示されています。
上では手動で曲げる最も簡単な方法について説明しましたが、以下では部品を機械的に曲げるための装置について説明します。 もちろん、膨大な量の機器を 1 つの記事でカバーすることは不可能なので、すべての機器を説明することはできません。 しかし、私は機械曲げのための主な装置について説明しようとします。そして、親愛なる読者がクリックすることによって、別の記事に移動してより詳細に研究することができる適切なリンクがいくつか与えられます。
金属を機械的に曲げるための装置および装置。
デスクトップアクセサリ手動駆動による曲げ加工に。 図10に示す装置では、ワークピースはテーブルと上部容積測定バー2との間にクランプされ、ワークピースの端が折り曲げられた端の幅に等しい距離だけ突出する。
また、パーツ上の棚の曲げは、ハンドル 1 を回すことによって実行されます。このタイプのより高度な機械では、テーブルとトップバーの間の距離を調整することによって曲げ角度を変更できます。
シート材料で作られた部品の端をさまざまな形状に曲げるための卓上装置には、右の写真に示すジグマシンがあります。
圧着機については別記事で詳しく書いていますので興味のある方は読んでみてください。
一部のジグマシンは、テーブル(クランプを使用)と床、プロファイルパイプから別に作られた表彰台(右の写真のように)の両方に取り付けることができます。
シートベンディングマシン。 これらの機械には、主にシート材料を縦方向に曲げるために設計された曲げ機械が含まれます。
機械機構の 1 回のストロークで、1 つの簡単な操作が実行され、シート材料を図 11 a に示すプロファイルに曲げることができます。 さらに複雑なプロファイルは、機械上で複数の操作で曲げられます。
機械自体は図 11b に示されており、テーブル 3 を使用して互いにしっかりと接続された 2 つのラック 1 で構成されています。機械にはクランプクロスバー 4 と回転クロスビーム 5 があります。
軽量クラスの機械では、ハンドル 2 を使用して手動で最大 180 度の角度でトラバースを回転します。重量クラスの機械では、トラバースの回転は機械式または油圧駆動によって実行されます。
曲げ加工は、シート素材をテーブル3上に置き、トラバース4で押し付け、回転トラバース5を回転させることにより、シート素材の端を必要な角度に曲げます。
最も単純なシート ベンダー (機械) には、ここでその製造について説明したシート ベンダーが含まれます。
プレスブレーキ。 プレスブレーキを使用すると、さまざまな曲げ作業を迅速、効率的、正確に実行できますが、コストが高く、寸法と重量が非常に大きいため、通常は生産で使用されます。
これらは、エッジの最も単純な曲げから、1 つまたは複数の平面で異なる角度で、またはさまざまなタイプの滑らかな曲線に沿って複雑なプロファイルを曲げるまで使用されます。
さまざまなプロファイルの曲げは、ラム 2 (図 12a および右下の写真を参照) を使用して実行されます。ラムはスライダー フレーム 1 に取り付けられ、ラムは材料をマトリックス 3 に押し込み、マトリックス 3 はスライダー フレームに取り付けられます。ライニング 4 をプレート 5 の上に置き、プレスします。
もちろん、パンチの形状や曲げ半径は、完成部品の形状の要件に応じて異なります。 マトリックスの作業部分は、ほとんどの場合、正方形または長方形の溝の形状で、かんな盤で削り取られます。
プレスブレーキ: a - ラム、b - ダイ。
異なる形状のいくつかのマトリックス2およびダイ1が図12bに示されているが、もちろん形状は異なっていてもよい。
複数回の曲げで必要な金属曲げプロファイルを得るには、曲げ加工を複数の段階で実行し、そのたびにブランクシートを設定停止位置まで移動させます。 トランジションの数は、生成されたプロファイルのキンクの数と同じです。
メカニカルプレスとユニバーサル金型。 小型部品の機械的曲げには、通常、従来の機械プレスが使用されます。 また、連続生産または小規模生産では、いわゆるユニバーサル金型を使用するのが合理的です。 このようなスタンプの例を図 13 に示します。
このようなスタンプの主な動作部品は、異なるプロファイルとマトリックス1を備えた交換可能なラム2です。90度のコーナープロファイル(または別の角度)を持つ曲げ部品の場合、マトリックスは正方形のプリズムであり、その側端に沿ってさまざまな厚さのブランクを曲げることを目的とした、さまざまな深さの角度のある溝。
図13からわかるように、溝(必要な曲げサイズに対応する)がパンチの方向(つまり上)を向くように、マトリックスはプレート3に固定されています。 そして、母材の横方向のずれは、スラブに固定された2つのラックによって防止されます。
そして、特定の半径で機械加工された作業輪郭を備えたラム(変更可能)を I セクションポンドホルダーの溝に挿入し、そこにボルト(ラムの長さが足りない場合は複数のボルト)で固定します。パーツは十分な大きさです)。
図 12 に示すダイでは、シート材料を異なる半径に沿って、異なる角度で曲げることが可能です。 後者の場合、追加のプランジャーとダイのセットが、将来の部品のプロファイルに対応する必要なプロファイル セクション (必要な角度) で作成されます。
板曲げローラー。 プレートベンディングローラーを使用すると、シート (バー) 材料をパイプ、ハーフパイプ (クォーターパイプなど)、および円錐の形状に曲げることができます。
金属曲げ - シート曲げローラー:
a - 4 ローラー バージョン、b および d - 3 ローラー バージョン。
プレート曲げローラーは、回転運動が与えられる 2 つの下部ローラーと、曲げられた部分を除去できるようにヒンジ付きベアリングに取り付けられた 1 つの上部ローラーで構成されます。 上ローラはワーク(鋼板)との摩擦力により回転します。
上部ローラーは、鋼板を曲げるときに必要な曲げ半径を与えることができるように、高さを移動する機能を備えています。 円錐面の部品を作成する必要がある場合は、上部ローラーに必要な傾斜を与えます (ローラー昇降機構を片側のみ回転させることで)。これは円錐面の母線の傾斜に等しいです。
下部の 2 つのロールの駆動は、手動 (ハンドルを使用) またはリミット スイッチ付きのペダルを踏んでギアボックス付きの電気モーターを使用して行うことができます。
規格外のベンディングマシン。 別のグループは、左側の写真に示されている非常に便利なマシンによって代表されます。 これにより、板金を溝に曲げることができるだけでなく (トップ ローラーにゴム リングを配置した場合)、さまざまな凹凸を転がすこともでき、その他多くの便利な特性があります。
また、英国製ホイール (説明したように、右の写真に示されています) に簡単な取り付けを行うと、この機械を使用してロッド、アングル、その他のプロファイルを曲げることができます。
パイプ曲げ機 - パイプベンダーについては、誰でも読める別の記事も書きました。
パイプ ベンダーのさまざまな設計オプションを説明および示し、パイプ曲げプロセス自体についても説明します。 そして、この記事が、何らかのプロファイルの金属を曲げる必要がある初心者の職人にとって役立つことを願っています。皆さんの幸運を祈ります。
にカテゴリー:
金属の曲げ伸ばし
曲げ加工に使用される設備、工具、装置
曲げのタイプは、たとえば、ステープル、ヒンジ、ブラケット、リング、およびシート、ラウンド、異形金属で作られたその他の製品の製造における図面の要件によって決まります。
ワークピースは、角度を付けて、半径に沿って、および成形された曲線に沿って曲げることができます。
手動曲げは多くの場合、万力を使用して行われます。 配管工のハンマーさまざまなデバイスを使用して。 入手用 正しいフォーム曲げ加工の際、整備士は特別なマンドレルを使用して、複雑な形状のワークピースや部品を曲げることがよくあります。 この装置は、同一部品のバッチを曲げる場合に特に広く使用されています。 操作の順序は、輪郭のサイズとワークピースの材質によって異なります。
曲げは、サンプルに従って、その場で、マーキングに従って、およびテンプレートに従って行うことができます。
細い帯状の金属やワイヤーから部品を曲げて作成する場合、小さな部品をつかんだりクランプしたり保持したりするためにペンチが使用されます。 クランプの最終的な形成は、ハンマーを使用して万力内のマンドレル上で実行されます。
米。 1. 薄いストリップ金属とワイヤを曲げる技術: a - 万力のマンドレルにペンチを使用してクランプを曲げます。 b - ワイヤーの耳を丸ペンチで曲げます。 c-ラジオペンチ(ニッパー)でワイヤーを切断する。 Gフィニッシュクランプ
ラジオペンチはワイヤーを曲げるときに使います。 ペンチとの違いは、顎が丸い円錐形であることです。 断面3mmまでのばねや棒を製造する工程では、ラジオペンチを使って線材を切断します。 この点ではコンビネーションプライヤーの方が便利です。 掴んだり、つまんだり、保持したりすることができます。 小さな部品、薄い部分のワイヤーやロッドの切断も可能です。
条件中 現代の生産主にプレスブレーキ、シートベンディングローラー、ユニバーサルプレスブレーキ、ベンディングマシンなどを用いて機械曲げ加工が行われます。
プレス ブレーキは、エッジの曲げから 1 つまたは複数の平面でのさまざまな角度でのプロファイルの曲げまで、さまざまな作業を実行するために使用されます。
プロファイルの曲げは、スライダー フレームに取り付けられたパンチと、プレス プレートのライニングまたはプレートに直接取り付けられたマトリックスを使用して実行されます。 パンチの形状や曲げ半径はさまざまです。 マトリックスの作動部分はソケットであり、通常は正方形または直線の溝の形で作られています。
米。 69. 金属板を曲げるためのプレス (a、b) と曲げに使用されるパンチとダイの例 (c)
曲げ加工に使用されるパンチとダイのさまざまなプロファイルの例を図に示します。 2、e。
多数の曲げで必要なプロファイルを得るには、設定された停止位置まで毎回シートのブランクを前進させながら、曲げをいくつかの遷移で連続的に実行します。 トランジションの数は、プロファイル上のキンクの数と同じです。 シートの曲げはシート曲げローラーで行われます。
曲げプロファイル用 さまざまなセクションローラーベンディングマシンが使用されます。 汎用の 3 ローラーおよび 4 ローラー曲げ機では、異なる曲率半径のプロファイルが曲げられます。
図では、 3、a はシートから作られたプロファイルを曲げるための 3 ローラー機械を示しています アルミニウム合金厚さは2.5mmまで。
2 つの下部ローラーに対する上部ローラーの調整は、ハンドルを回転させることによって実行されます。 曲げるときは、ワークピースを上部のローラーで下部の 2 つのローラーに押し付ける必要があります。 クランプは、ローラーがプロファイル フランジに沿って自由にスライドするように取り付けられており、曲げプロセス中にローラーがねじれるのを防ぎます。 製造中のプロファイルワークピースに傷や傷がつかないように、ローラーの表面は高度に研磨する必要があります。 大きな曲げ半径を持つプロファイルは、3 ローラー機械でいくつかの段階を経て曲げられます。
円、螺旋、またはさまざまな曲率の曲線の輪郭の形状のプロファイルは、4 ローラー機械で製造されます。 4本ローラーマシンは、内部に駆動機構を備えたフレーム、ワークを送り出す2本の駆動ローラー、ワークを曲げる2本の加圧ローラーで構成されています。 ハンドルを回転させることで、必要な曲げ半径を設定します。
パイプ曲げ 小さいサイズさまざまなデバイスを使用して手動で実行できます。
大量の作業では、コイル巻きパターンに従って動作するパイプ曲げ機が、直径 10 ~ 400 mm のパイプ (特に薄肉パイプ) の曲げに広く使用されています。 ローリング曲げ法とは対照的に、スライダは静止または長手方向に移動しながら、曲げテンプレートに回転が与えられます。
ワインディング法による曲げ加工装置の機構は、曲げテンプレート、クランプ、スライダー(支持ブロック)から構成されます。 ほとんどの場合、楕円形や波形を防ぐためにマンドレルも使用されます。
最も普及しているマンドレルは、 以下のフォーム:スプーン形(I)、球形(III)、または切頭球形(II)。 薄肉パイプを曲げる場合は、複合マンドレル (IV) が使用されます。 このようなマンドレルはパイプ壁をサポートします。
米。 3. 曲げプロファイル用の 3 ローラー (a) および 4 ローラー (b) マシン
米。 4. マンドレルを使用したパイプ曲げのスキーム
本機の操作手順は以下のとおりです。 パイプを曲げテンプレートの溝に取り付け、クランプを使用して直線部分に取り付け、スライドを調整します<3, которым труба во время гибки прижимается к гибочному шаблону. Приводимый во вращательное движение гибочный шаблон увлекает за собой трубу, которая, находясь в ручье между шаблоном и ползуном, снимается с дорна и изгибается на необходимый угол и радиус.
鉄および非鉄金属から湾曲パイプを大量生産する最も生産的な方法の 1 つは、金型曲げです。 金型は油圧、空圧、摩擦プレスに取り付けられます。
建設中やその他の家事中に、金属を曲げて特定の形状にする必要がある場合があります。 プロのブリキ細工師は、このための特別なツール、シートベンダーを持っています。 しかし、自分の手と即興の手段以外には何も持たない家の職人はどうなるでしょうか? 曲げ工具を購入するべきですか、それともレンタルするべきですか?
これは何もする必要がないことがわかります。 必要なのは、少しの工夫と、すべての家庭職人が自宅に持っている基本的な設備だけです。 もちろん、金属板の厚さが 3 mm を超えない限り、曲げ加工は楽しいプロセスです。
ベンダーを使わずにシートを曲げる
自宅で金属板を曲げる方法を説明するいくつかのオプションを見てみましょう。
曲げるための手工具として、定規、チョークまたは鉛筆、万力、木のブロック 2 個、スチールアングル、ゴムハンマーを使用します。 金属板を曲げるには、湾曲する端がテーブルから突き出るように作業テーブル上に金属板を配置する必要があります。 まず、曲げストリップに定規に沿って印を付ける必要があります。 折り目マークはデスクトップの端の線と一致する必要があります。
テーブルの端をスチールのコーナーで覆います。 木製ブロックを使用して金属シートの両側を万力で固定します。 シートの突き出た端を曲げ始め、ゴムハンマーで叩き、最初は一方向に、次に反対方向に、ある隅から別の隅に徐々に移動します。
曲がった端が完全に下がり、テーブルの端に固定されているスチールの角に平らになるまでハンマーで叩きます。 つまり、角度は 90 度でなければなりません。 この方法では、厚さ 2 mm までのシートを曲げることができます。
たとえば、これは簡単な庭のバーベキュー用の箱を作る方法です(もちろん、角は後で溶接する必要があります)。
重要なヒント: ゴムハンマーがない場合は、通常のハンマーを使用できます。 次に、木のブロックまたはテキストライトプレートを通して端を打ち落とす必要があります。 この場合のみ、曲げた端にハンマーの跡が残りません。
オプション 2
薄い金属シート (0.8 ~ 1.2 mm) を素早く曲げる必要がある場合は、通常のペンチを曲げツールとして使用できます。 定規、鉛筆、平らな木のブロック、ゴム製ハンマーまたは耐久性のある木製ハンマーも必要です。 一連のアクションは次のとおりです。
- 金属シート上で、定規を使用して将来の折り目の端の輪郭を描きます(線は鋭利な物体でさらに少し押すことができます)。
- シートの端が正確にマーキングラインに来るように、ペンチでシートの端をつかみます。
- マーキングに沿ってペンチを徐々に動かし、端を上に曲げます。
- 曲げ角度が 90 度に近づくまで繰り返します。
- 角度を正確に合わせるために、曲げたシートを木のブロックに「置き」、角度の正確な形状が得られるまでハンマーで叩きます。
このようにして、シート ベンダーを使用せずに、たとえばブリキの鋳造品にエッジを作成できます。
自分だけのローラー
金属シートからパイプを独自に製造する必要がある場合があります。 手作りのパイプは、煙突、空気ダクト、サモワールパイプなど、さまざまな目的に使用できます。職人は、板金をパイプに曲げるさまざまな方法を考え出しました。 最も単純なオプションをいくつか見てみましょう。
オプション1
金属を曲げるための特別な装置がなくても、ある種の丸いブランクまたは既製の古いパイプの一部を使用して、シートをパイプの形状に丸めることができます。 ほとんどの人はパイプを使用します。
そこで、土やコンクリートの床の表面に金属のシートを敷きます。 次に、金属を巻き付けるテンプレートを準備しましょう。 古いパイプの両端に2本の小さなチューブを十字に(互いに直角に)溶接します。 直径はバールを差し込むのに十分な大きさでなければなりません。 これが曲げ加工装置になります。
次に、パイプをシートの端に置き、シートを巻き付け始めます。 この作業には 3 人が必要です。1 人はパイプの上に立ち、残りの 2 人はバールを使ってパイプを回転させます。 各回転は 90 度実行されます。 バールは 0 度に再配置されます。
そこで、シート全体をパイプの周りに徐々にねじり、新しい円筒形の回転を数回繰り返します。 通常、シートの端はまっすぐなままです。 曲げる場合も金属製の曲げ器具として木槌やゴム槌が必要です。
必要な直径のパイプを取得するには、巻尺を使用して円周の長さを測定し (これを行うには、直径に 3.14 を掛けます)、必要な部分をグラインダーで切り取ります。 この後、ワークピースからパイプを取り外し、新しいパイプの継ぎ目に沿って溶接作業を実行します。 このように、特別なシートベンダーを使用せずに、好きなだけパイプを作成できます。
オプション 2
ボイラー室にパイプを設置するには、亜鉛メッキ金属を使用することをお勧めします。 また、熱間圧延鋼材はしわがなく滑らかな曲げが得られるため、丸パイプの製造に使用されます。 冷間圧延鋼はより脆く、より優れたプロファイルの製品を製造します。
金属を曲げ始める前に、シート全体から一部を切り取ります。その幅は、将来のパイプの円周に折り目部分の3 cmを加えたものに等しくなります(これは金属シートの端の接合部の継ぎ目です)。 ; セグメントの長さはパイプの長さと同じです。
この作業を自分で行わなければならない場合は、ブリキだけではうまくいかないため、長さを 1 メートル以上にしないことをお勧めします。 最終的な長さを長くする必要がある場合 (たとえば、2 メートル)、2 つのセクションを溶接で接続する必要があります。
作業は耐久性のあるテーブルで行われ、その端に鋼製のコーナーが配置され、シートベンダーとして機能します。 ラペルラインは、鋭利な物体を使用して金属ブランクの長さに沿って描かれます。 テーブルの端と組み合わせて、木槌で下に向かって叩きます。 次に、裏返して端をシートの上に完全に曲げます。
次のステップ: 裾から 2 mm 後ろに下がり、最初の線と平行に別の線を引き、折り目を再び下に折ります。 ワークピースの 2 番目の面でも同じことが行われます。 パイプが形成された後、これらの曲がりは「ロックに」接続されます。 外部の助けを借りずに単独でパイプを曲げる方法は、次のアドバイスが役に立ちます。ワークに沿って中心線を引き、直径より小さいパイプ上にシートを置き、中心線から始めて、順番に切断します。セクションの周りでシートを曲げます。 長い端を一緒に固定し、木槌で叩きます。
完成したパイプの直径を確認し、必要に応じて通常の金属ハンマーを使用してパイプを次のセクションに接続するための「フランジ」を作成します。 新しい亜鉛メッキのエアダクトが完成しました。
このレビューからわかるように、どの所有者の家にもある金属を曲げるための最も簡単なツールを使用して、自分でブリキの加工をうまく行うことができます。 シートを曲げる独自の実績のある方法はありますか? 私たちのページで共有していただければ幸いです。